Shake Things Up In Our Reliability Lab
When we say we test everything past the point of failure, we mean everything! That includes the mounting system and brackets on our electrical components. Some might question, “Other than being fun to watch, what do you hope to learn from putting products through that type of testing?!” The answer is twofold: Our displays are […]
Justin Ochsner on 5/5/2017
Categories: Pro Sports and Colleges, Sign Company News
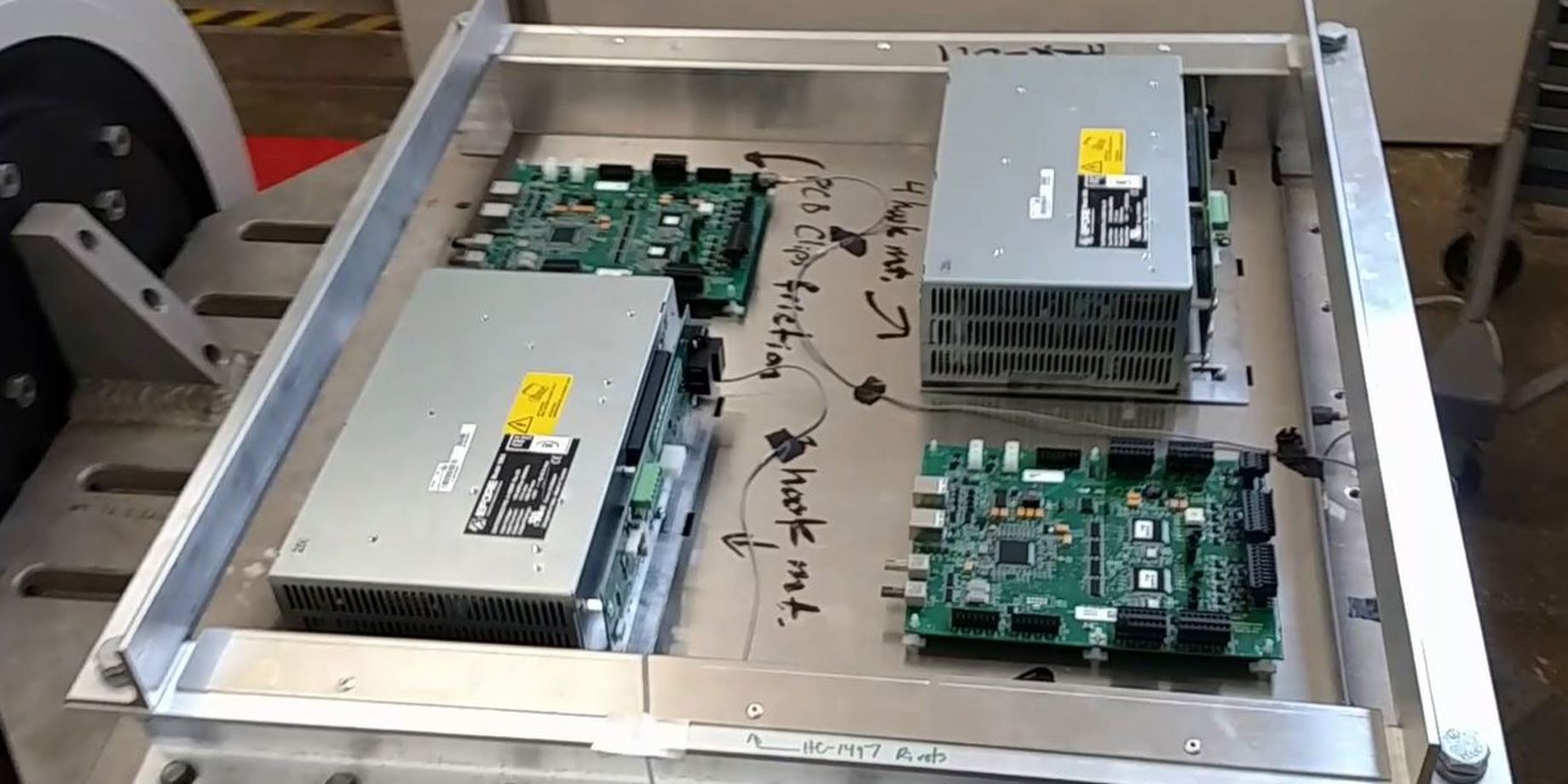
When we say we test everything past the point of failure, we mean everything! That includes the mounting system and brackets on our electrical components.
Some might question, “Other than being fun to watch, what do you hope to learn from putting products through that type of testing?!”
The answer is twofold:
- Our displays are transported to their final destination after being manufactured in Brookings, South Dakota. We want to know if the vibrations and shaking and bouncing and stop-and-go of transportation will cause problems with the mounting system and brackets that hold together certain pieces of our displays.
- If we can cause the mounting system and brackets to fail, we can learn where they fail and why. This information helps us learn from the failure and then allows us to use improved parts in the future.
Everything done in our reliability lab is to make our displays better so they can last longer and provide our customers with a safer, more reliable purchase. Accounting for transportation is one aspect that many customers and display manufacturers might not take into consideration. We think of those details to put our customers’ minds at ease.
Shannon Mutschelknaus works in Daktronics Quality & Reliability Lab Services and noted, “Not all customers have ‘average’ roads leading to their facilities, so it’s valuable to know the margins between ‘average’ and the actual levels of stress that will cause something to break. Many customers have rough service roads leading to their installations and they expect our products to work when they get there.”
We start off at lower levels of vibration and impact (think ‘average’ roads) before working our way up to the more extreme levels (think service roads). Some might say, “If it ain’t broke, don’t fix it.” Our reliability lab has a different saying, “If it ain’t broke, let’s break it and find out how to make it better!”
This article is by Justin Ochsner
in Live Events Marketing.
Connect via LinkedIn