Discussing Daktronics Repair Center with Trent Erickson
Where do your LED sign and video display parts go to be repaired? Daktronics repair center is in Sioux Falls, South Dakota, USA.
Justin Ochsner on 6/24/2020
Categories: Business & Community, Out of Home Advertising, Sign Company News, Spectaculars

Matt and I recently sat down Trent Erickson, Daktronics Repair Center Plant Manager, for a conversation on The Daktronics Experience podcast. We discussed our US-based and global repair centers, how they operate to serve our customers, and some of the common and uncommon reasons for displays to be repaired. Here are some of the main points from the conversation.
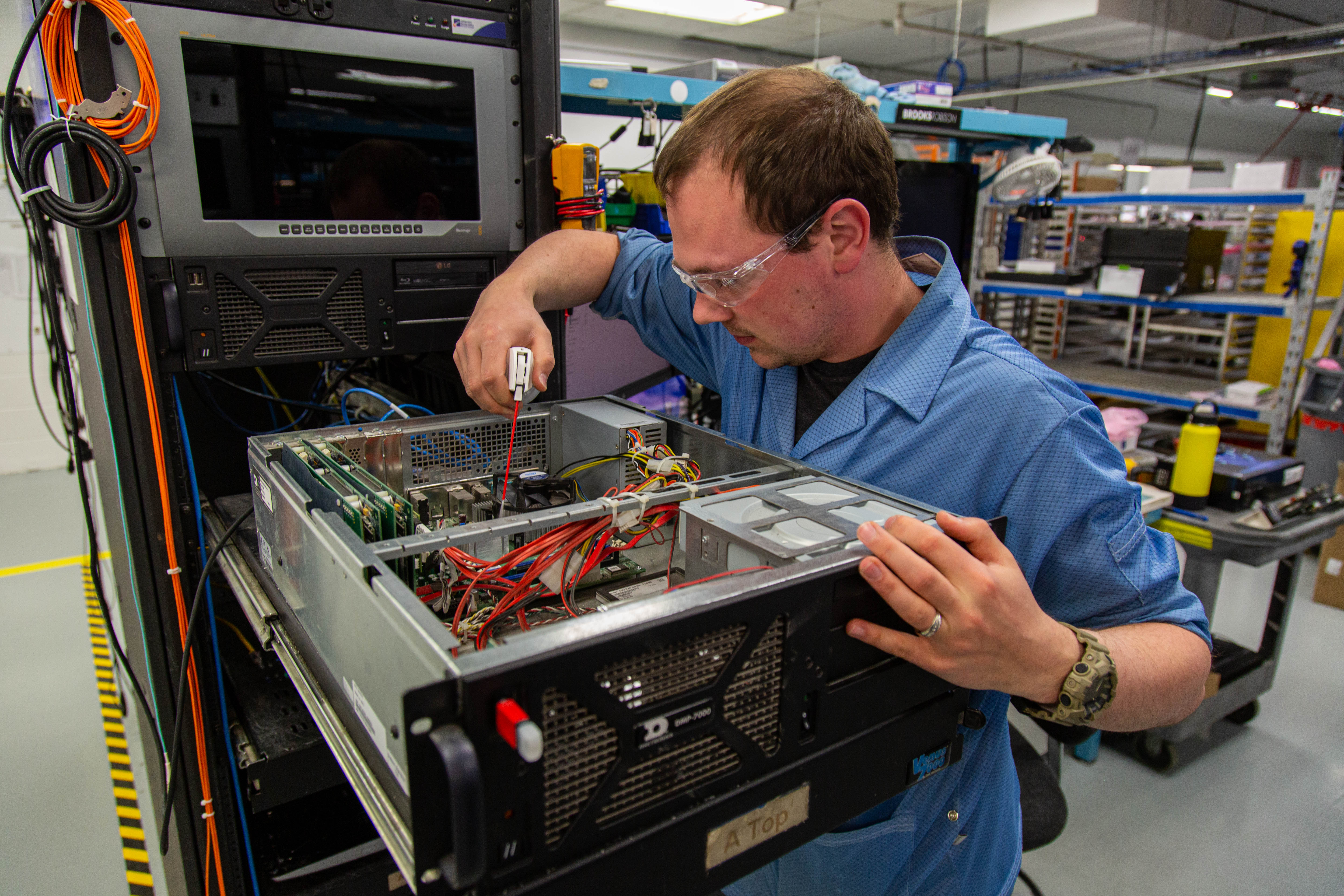
Justin: Trent, can you give us an overview of the Daktronics Repair Center?
Trent: Yes, our corporate office for our repair centers is located here in Sioux Falls, South Dakota. We have regional offices as well in Canada, Ireland, Shanghai and Australia. Here in the corporate repair center, we repair any products that have been set up as repairable products. Some examples would be control systems, controllers, modules and potentially exchange equipment as well. We also help coordinate vendor repairs, things like cameras, amps and sound system equipment.
Matt: I didn’t realize vendor gear was something Daktronics would repair.
Trent: Yes, over the years we’ve had quite a bit of different suppliers that we’ve worked with where we will either do some troubleshooting, a firmware update or we will coordinate with them to do the return materials authorization back to the supplier and get that equipment out to the customer.
Justin: Many of our customers are surprised to hear that we have a repair center based here in the United States. Can you tell us a little bit about why that is important for our customers?
Trent: We know through customers on the service and sales side that it is very important. It allows us to shorten our lead times and many times turn things within a week. Our standard turnaround time is closer to about two weeks, but if you had to send something internationally you would spend that amount of time just shipping one way or another. So, it also saves a significant amount of money in shipping costs since we are right here in the United States.
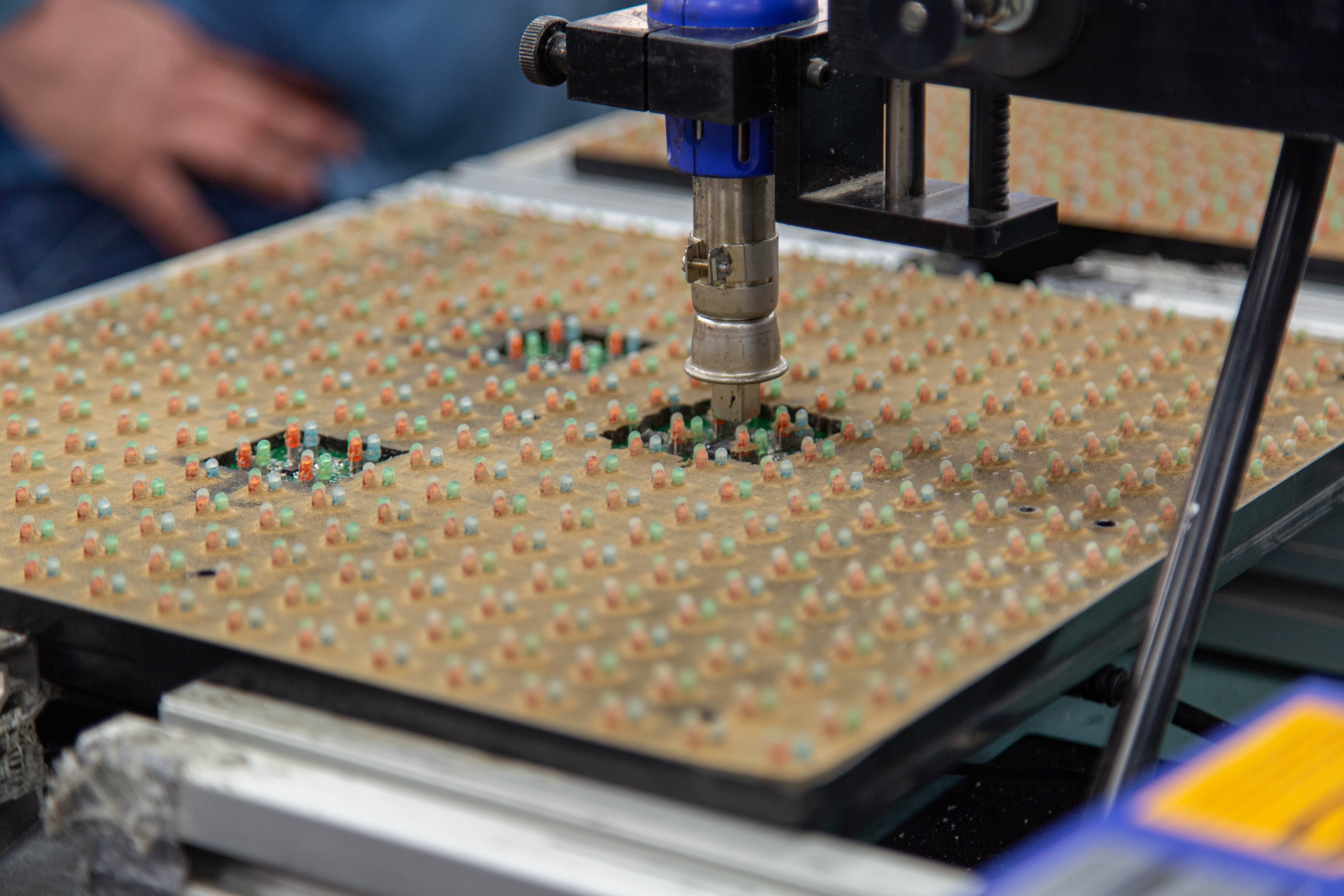
Matt: I heard that 94% of the parts that come into the repair are able to be reused and that only 6% of the parts need to be scrapped. Is that correct?
Trent: That is correct for what we have been trending over the last couple of years. We find that the majority of the ones that need to be scrapped have had something environmental happen to them. Some odd examples we have seen are displays that have been hit by lighting or shot with a bullet. But yes, 94% are able to be repaired.
Matt: Do you work closely with both design and engineering teams as well?
Trent: Yes, we do on both sides. As they are developing new products, we work pretty closely with all the design engineer groups to make sure it is serviceable and that we would be able to successfully repair many of the products that come through. And then on the backside, as we are doing those repairs, we track all of the information including what was wrong with the parts that came in and what did we do to fix it? Then, that information will go back to both manufacturing and design engineering so both can continue to improve their processes.
Justin: So, we have a lot of different climates and environmental things that could occur across the United States that could cause a display to be in need of repair. You’ve mentioned some things, but what are some other reasons a display might need to be repaired?
Trent: Well, we would have some weather-based reasons, but most of our products are very good in inclement weather. They’ve gone through hurricanes and tornadoes, and events like that will cause some significant damage. With hail on the front of a sign, it really depends on the severity. With softball-sized hail, you’re going to have to replace the sign. Lightning, on the other hand, is always a difficult one. With a direct shot of lightening, you’re most likely going to have to call your insurance company in that situation.
Other more obscure things we’ve seen are birds’ nests, squirrels’ nests, beehives, things like that inside the sign that eventually cause something to short out. One of the wackier displays we’ve repaired was in Australia. There were some birds pecking out the LED’s and eating them.
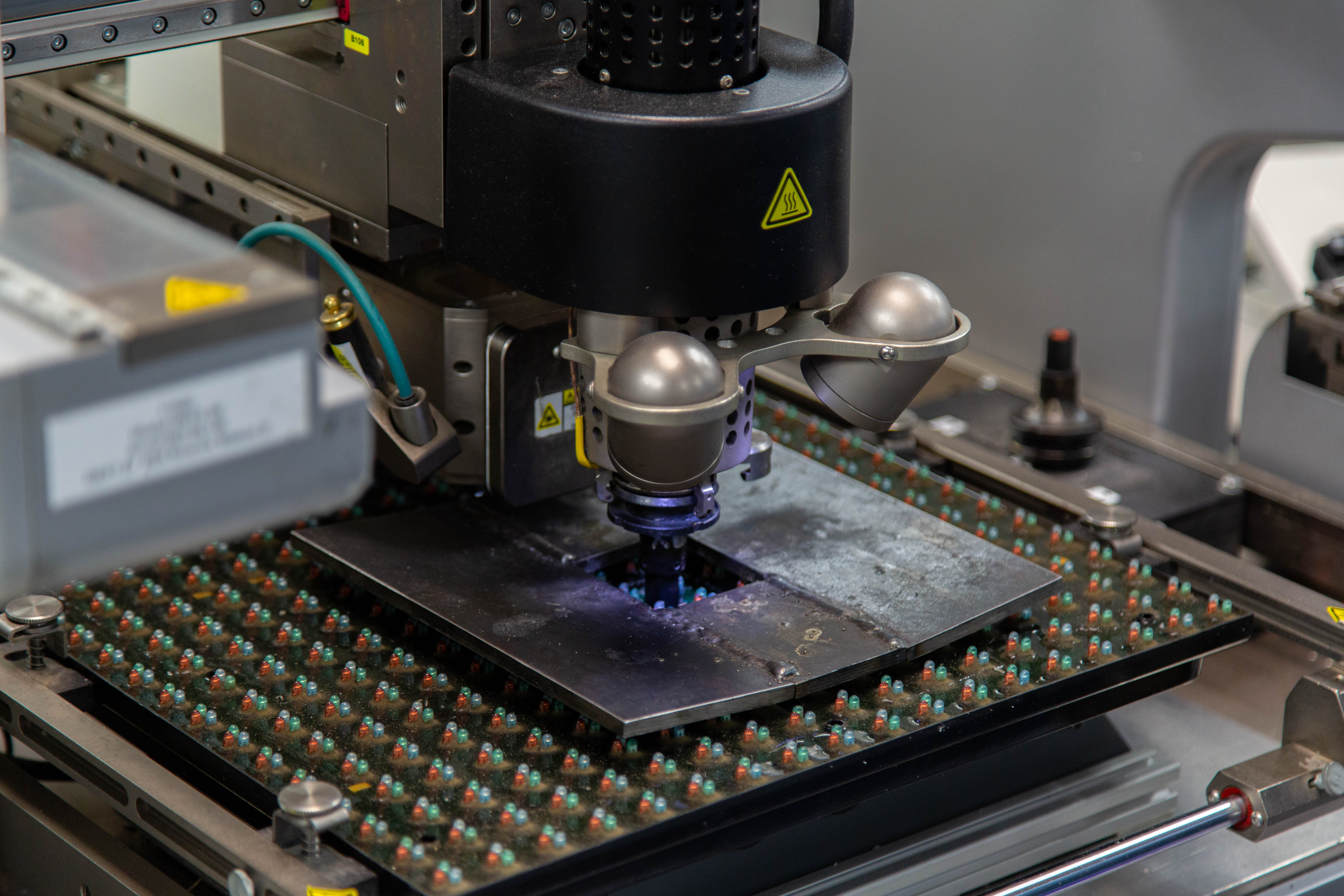
Matt: In many cases for our customers, being able to ship a part and get it back quickly is so important. You always want to get things back up and running as soon as you can.
Trent: Yes, we are constantly trying to improve that as well. And our success rate is good on making sure we’re getting all events covered and always trying to make sure we can improve not only on our lead times but also our critical turnaround times while making sure everyone is working with their coordinator or account manager and we will do whatever we can.
To hear more details about our repair center, check out the full conversation with Trent by clicking here.