Daktronics Lab Services is our in-house testing facility, located at our headquarters in Brookings, SD. Here, we do everything from measure image quality, test performance and even stress components to complete failure to discover vulnerabilities. Our engineers use this data to improve and develop our indoor and outdoor products to ensure every display is built with unmatched integrity, quality and reliability.
Daktronics provides end-to-end high-quality testing on components based on decades of experience around the world. This far exceeds typical compliance requirements, which often fall short of customer expectations.
Why Do We Test Differently?
Displays are complicated, which is why we test at many levels, from full displays to individual components. If your display doesn't function properly, the consequences could be as harsh as bad press coverage and lost revenue or as dire as chaos on the road.
Daktronics has thousands of digital LED video display technology installations around the world. Our rigorous testing procedures provide peace of mind that each one performs exceptionally for every moment that matters during its entire lifespan.
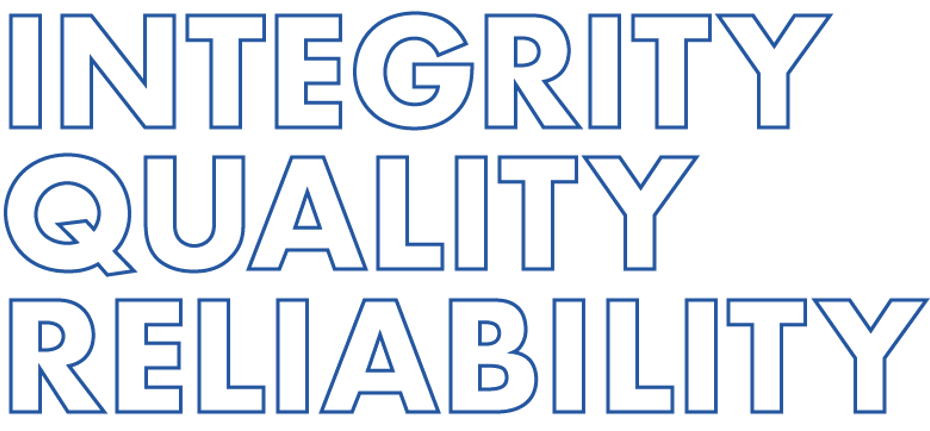
Our Testing Process
Our Lab Services professionals are dedicated to their craft, collaborating with each other to draw on a wealth of knowledge and experience, using state-of-the-art equipment. The following represents a sample of our comprehensive testing process.
Integrity Testing
By exposing components to various conditions, we measure the integrity of product performance characteristics such as optical properties, power usage, efficiency and much more.
Light and Image
We measure light output and color properties of modules in the Image Quality lab. This provides performance data so we know exactly how the display will perform from any vantage point, as well as evaluate how our product design stands up to challenges such as sunlight or overhead lighting. We can even provide 3D photometric files for lighting designers who want more details.
Color and Contrast
Examining the luminous flux and color properties of individual LED samples in the Integrating Sphere helps verify supplier specifications.
We use a controlled environment and consistent lighting conditions to measure the effects of ambient light on contrast performance – one of the best indicators of a display’s contrast in real-world environments. This is listed on spec sheets as ambient contrast ratio (ACR).
Compatibility and Thermal Performance
We use an electrical radiation absorbing chamber to ensure products comply with federal and international regulations on electromagnetic noise, so our equipment won’t interfere with internet, radio or cellular signals.
The large-scale environmental test chamber verifies display heating and cooling systems using a full wall of lights to simulate full sun exposure on our products so we can determine reactions to heat and solar radiation and ensure products will keep working in all environments.
Quality Testing
These types of tests make sure products we send out the door are consistently constructed to Daktronics standards.
Consistency
Display cabinets, modules and other components need to meet tight requirements. We use our Coordinating Measurement Machine to test aluminum and steel sheet metal, aluminum extrusion, plastic louvers and housings, and even the bends in metal measurements, down to a tolerance of ±3 micrometers.
Cleanliness
Our C3 (Critical Cleanliness Control) enables us to detect corrosive elements (such as salts) in electronics and other components from our suppliers. This helps determine where the elements are introduced during the manufacturing process, eliminating issues right within our factory.
Reliability Testing
By running our products through this series of tests, we determine how long they maintain their image quality as they age – so our customers can be confident they will look incredible for years to come.
Weather and Ultraviolet Light Challenges
To check and prevent degradation of materials such as plastic, silicone, epoxy, paint and LEDs, we expose them to ultraviolet light and condensation in our UV weathering tester.
The Temperature & Humidity Chamber simulates extreme environments to test component sensitivity to humidity, corrosion, hydrolysis and electrical changes. With temperatures ranging from -40°C to 100°C (-40°F to 212°F) and humidity levels between 10% and 98%, the test provides insight into expansion resilience and solder bond strength.
Water Resistance
Our modules have to stand up to heavy rain and wet conditions. We take water testing to new depths, with pressurized 360° water jets that spray enclosures, specialized water detection inside the components, and even submerging modules under a meter of water for 30 minutes to replicate severe conditions.
The salt fog chamber simulates coastal air conditions by creating fog with a 5% salt solution and an ambient temperature of 95°F (35°C). Components endure prolonged exposure to assess their capacity to withstand corrosive effects common in these environments. This testing provides the knowledge to create components that enable our displays to be installed pool side, or outdoors in rainy or coastal climates – even in regions more susceptible to extreme weather such as hurricanes, torrential rain, and flooding.
Supplier Testing
Part Verification and Failure Analysis
Testing is crucial when vetting new vendors, purchasing from a distributor rather than a manufacturer, and when supply chains are tight. We scrutinize components, design and materials to verify their authenticity.
Also, when there are emerging designs and technologies in research and development, the Lab thoroughly examines them to ensure they live up to expectations.
If parts fail in the field, we analyze them in our failure analysis lab to determine the cause so we can fix the problem and prevent it from happening again.
A Look Inside the Lab...
Schedule Your Tour
To see our testing in action, we invite you to contact your Daktronics sales rep to set up a tour. Or fill out the form below so we can reach out to you.